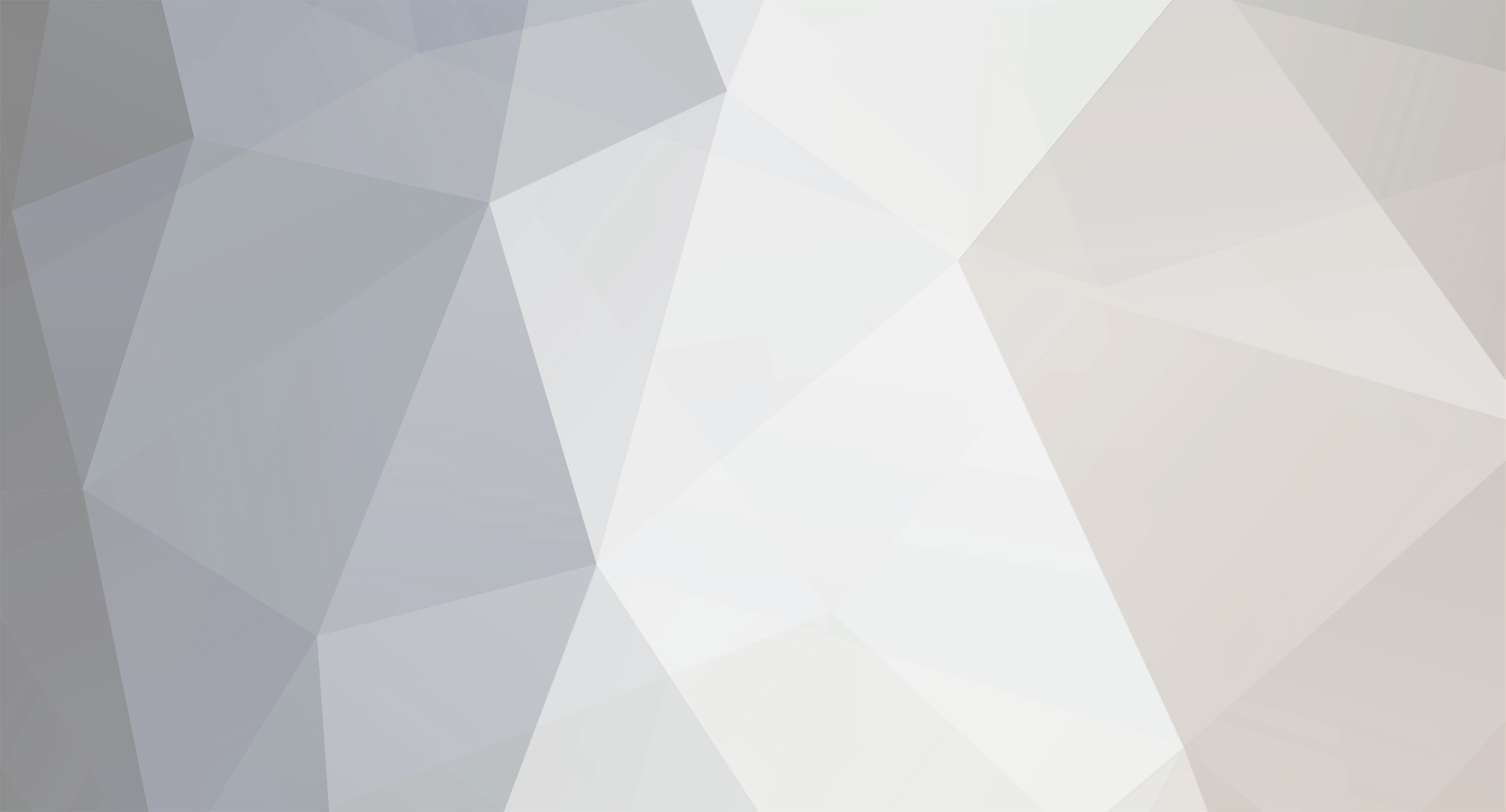
BorgelMorgel
Members-
Gesamte Inhalte
147 -
Benutzer seit
-
Letzter Besuch
Alle erstellten Inhalte von BorgelMorgel
-
Drezahlmessung mit TF?
Thema antwortete auf BorgelMorgels Suggy in: Projektvorstellungen und Projektideen
Hab in den vergangenen Tagen einige Tests mit optischen Drehzahlsensoren durchgeführt. Hatte zwei zur Probe. Der Erste gibt Spannungsimpulse aus, der Zweite einen konditionierten Strom von (4...20)mA. Hab mit dem DC Brick einen Gleichstrommotor gesteuert und die Geschwindigkeit über den LinearPoti geregelt. Auf die kleinen Scheibe ist ein Reflektionsstreifen geklebt. Bei Kontakt wird das ausgesendete Licht zum Sensor zurückgeworfen. Die Impulse hab ich über den I/O 16 erfasst. Strom musste ich mit dem Multimeter messen, da ich leider kein Current-Bricklet zur Hand hatte. Auf dem LCD hab ich mir dann noch paar Werte anzeigen lassen. Hab noch einen weiteren Sensor in der mache der auf ein anderes Prinziep setzt. Bei geeigneter Kalibrierung kann man so aber ganz gut die Umdrehungen messen. Anbei noch ein Bild vom Aufbau. -
Super! Hab die FW 2.0.1 drauf gemacht und das Beispiel "Find_Borders" ausprobiert. Bei mir funktioniert jetzt alles so wie es soll. Werde meine anderen Programme mal umstellen, aber das sollte jetzt alles passen.
-
Ich hab nach der Umstellung auf 2.0.0 auch Probleme mit dem Joystick Bricklet. Der erscheint ganz normal im Viewer (2.0.1) und ich hab auch die FW auf die aktuelle gestellt. Hab dann die exaples ausprobiert, also bloß meine UID eingetragen und bei dem "find corners" haut das nicht hin. bezieht sich immer auf die callback funktionen. Unten steht dann ein Timeout Error: in send_request raise Error(Error.TIMEOUT, msg) Error: -1: Did not receive response for function 9 in time Der meckert auch wegen der set_debounce_period(200) und dem set_debounce_period self.ipcon.send_request(self, BrickletJoystick.FUNCTION_SET_DEBOUNCE_PERIOD, (debounce,), 'I', '') Tritt das evtl. auch bei jemand anderen auf oder bin ich einfach nur Blind und hab wieder was vergessen. Hab im Beispiel selber aber nichts geändert, außer der UID.
-
So hab mal ein paar Schichten gemacht und bin auf ein kleines Problem gestoßen. Die einzelnen Schichten sind 2mm dick, deshalb bekomme ich keine geeignete Höhe für ein Brickstapel. Hab noch eine andere Idee die ich mal verfolgen will, vielleicht lässt sich das da lösen. Oder jemand hat noch eine Idee. Wollte ungern unterschiedliche Materialdicken nehmen und selbst wenn komme ich nicht auf die passende Höhe.
-
Der Laser befindet sich ähnlich wie bei einer CNC Fräse überhalb des Materials. Durch die Regelung der Energie des Laser kann man unterschiedlich tief in das zu bearbeitende Material eindringen. Aussparungen für Anschlüsse sind ale drin. Festigkeit erreicht man ja dann durch das Verschrauben oder Verkleben der einzelnen Schichten.
-
Na man muss halt schauen wie dick man die einzelnen Schichten wählt und da es ja Ringgebilde sind (Rechtecke) muss man in dieser Schicht an der entsprechenden Stelle eine Lücke lassen. MAl sehen ob ich morgen gleich dazu komme, im Bild wird das bestimmt verständlicher. Kann ja auch eine Zusammenbauanimation machen
-
@Nic Also der Lasercutter schneidet aus einer größeren Platte alle Einzelteie die man festgelegt hat. Die Höhe der Einzelteile wird über die Materialdicke bestimmt. Der Laser muss das natürlich schneiden können. Dann hat man einen Haufen Teile die man übereinander "puzzelt". Da die Bricks/ Bricklets ähnlich sind werden aber viele einheitliche Teile entstehen. Das schrenkt die Teilevielfalt einwenig ein und senk Produktionskosten.
-
Ich werde die einzelnen Sichten erst mal 3D modelieren und dann Schnittpläne anlegen. Werde mal Versuchen da was passendes für einen Stapel zu entwerfen, vielleicht hat ja einer die Möglichkeit, einen Prototypen fertigen zu lassen. In den vergangenen Tagen hab ich mir da einiges durch den Kopf gehen lassen. Ich denke für die Masse wäre das, das beste. Spezielle Gehäuse würde ich trotzdem mit dem 3D Drucker machen lassen. Vielleicht kann man sich ja ergänzen PS: Die STL`s werde ich also dennoch im Auge behalten!
-
@Nic Beim Lasercutter wird ein energiereicher Lichtstrahl zum schneiden verwendet. Ist sehr genau und man kann halt viele Teile in kurzer Zeit fertigen.
-
Was würde das fertigenlassen kosten? Wie dick ist so die standard Plastikplatte, (2, 4 oder 5) mm?
-
Was kostet das Lasercuten bei Kuststoffteilen?
-
Luxor warum rückst du erst jetzt damit raus . Die Idee ist auch gut. Ich werde mal sehen inwiefern sich das mit dem Gehäusetyp umsetzen lässt.
-
Hallo ispott, was genau möchtest du denn Messen bzw. was ist deine Aufgabe? Vielleicht kennt noch jemand eine passende Lösung. Ich mache Berufsbedingt auch einiges mit der verschiedensten Messtechnik, vielleicht kann man ja helfen. Gruß
-
Also der Abstand von 0,5mm ist nicht zur Lüftung gedacht, zumindest nicht vorwiegend. Über eine richtige Lüftung mach ich mir noch Gedanken. Luxor, wenn du deinen Drucker richtig eingestellt hast, können wir noch mal einen Probedruck machen. Diesmal geh ich noch mal alles durch, nicht das der Prototyp nutzlos ist. Mit dem Gehäuse denke ich kriegt man den Stoß- und Staubschutz schon hin. Spritzwasser wird schwierig, weil durch die Anschlüsse bedingt ja immer einige Öffnungen vorhanden sind.
-
Hab ein wenig weiter gemacht und einige Fehler korrigiert. Anbei zwei Bilder vom aktuellen Stand für das Stepper-Gehäuse. Die Wandstärke beträgt jetzt nur noch 2mm, der Brick wird an den Bohrungen ausgerichtet und hat jetzt in jede Richtung 0,5mm Luft. Auf der Seite des USB Ports beträgt die Aussparung sogar 1mm. HAb auch mal alle Lichtprofile der Anschlüsse betrachtet, sodass jetzt jeder Stecker genung Platz hat. Den Brick hab ich auch neu vermessen und aufgebaut. Es waren zuviele Fehler im Alten.
-
Der Pi, verbraucht doch sogut wie nichts
-
Ich sammel auch gerade Messdaten für Temp, Humi und Licht. Hab dazu eine kleine Pythonanwendung auch einem alten Rechner laufen. Die externe Hardware ist aber notwendig. Mit dem Pi wäre das aber eine solide, günstige und überschaubare Lösung. Das werde ich auch mal angehen. Für mich sind die gesammelten Messdaten erst mal nur zum gucken, um vorallem Grenzen für die spätere Reglung zu sammeln.
-
Danke jan für den Wiki Eintrag. Bin gerade am umarbeiten der Gehäuse. Loetkolben hat ganz recht, es muss klar sein wofür das eigentlich dienen soll, denn einen großen Vorteil von TF finde ich die flexibilität der Module. Die kann man nach belieben verstauen und anbringen. Eine IP Klassifizierung werde ich mir mal anschauen, was da möglich ist. Jenachdem wie genau man fertigen kann, wäre es ja zumindest Staub-, Stoß- und Spritzwassergeschützt. Was der Werkstoff ab kann, kann ich leider nicht abschätzen. Da wäre es gut wenn sich die 3D-Drucker-Besitzer mal zu äußern. Zu den Datein, also ich weiße an dieser Stelle mal klar drauf hin das die Datein mit einer Softwärelizenz erstellt wurden, die nicht kommerziell eingesetzt werden darf. Da es aber um private Anwendungen geht ist das egal, sollte aber dennoch von jedem der die Datein verwendet beachtet werden. Zum Format bin ich mit noch nicht ganz einig. Ich hab jetzt alles im Inventor gemacht. Bralph wollte gern andere Formate. Also STEP wird nichts bringen weil das nur ein Hüllenklumpen ist, dort kann man nichts mehr verändern. Wenn ich die Toleranzen richtig berücksichtige, sollte das für alle passen. Werde noch ein bischen experimentieren. Was ich auch interessant fand, war der Vorschlag mit der Hutschienenbefestigung. Zu Preis kann ich nicht viel sagen, bei professionellen Lösungen wären es ja nicht nur die Formen, auch die Ingenieurdienstleistung usw. treiben den Preis hoch. Wie gesagt viele werden überhaupt kein Gehäuse brauchen, aber für die, die eins wünschen finden wir eine Lösung. Es wäre gut wenn noch mal jeder seine Anforderung preis gibt, dann findet man ein Mittel. Gerade beim Stepper und Co wäre auch eine Belüftung notwendig!
-
Sehr schön das die Richtiung schon stimmt. Mir ist auch aufgefallen das die Anschlüsse manchmal etwas abweichen, weil der Bestücker nicht so genau arbeitet. Im gewissen Rahmen kann ich das berücksichtigen. Manchmal sind die Abweichungen aber schon gewaltig. @Bralph Könntest du mal ein paar Bilder von den Teilen reinstellen? Ich werde die Woche noch mal einiges Nacharbeiten und neue Datein erzeugen. Hoffe das es dann besser passt.
-
Ok, da mach ich 0,5mm Toleranz. Ist natürlich ne ganze Menge, aber dann passt das. Mit der Höhe könnte es Probleme geben weil die Bricks + Brickverbinder so ein komisches Maß hatten. Da bin ich glaube auf irgendwas mit ...,75mm gekommen. Passen die Radien, also konnte der das alles drucken? Gab es noch an anderen Stellen Probleme? Gruß
-
Mist, das wird vermutlich zu knapp bemessen sein. Glaube 0,05 oder 0,1. Passt der Brick rein? Was sind gute Maße für deinen Drucker? Also wie fein kann ich das planen (1 /0,5 / 0,25 ). Da mach ich die Gehäuseteile etwas größer um dann die Druckbreite zu berücksichtigen. Bei den Aussparungen hab ich 0,5mm als Tiefe gewählt.
-
Cool, da freu ich mich schon auf das Ergebnis. Hast du eigentlich noch was ändern müssen?
-
Hier die STL Datein und ein Bild vom Servodeckel. Boden.stl Deckel.stl Brick_40x40_Stepper_Gehaeuse.stl
-
Servus, so hab mal Deckel, Boden und Deckel für Servo Brick gemacht. Dabei ist mir ein kleiner Fehler aufgefallen den luxor mit gedruckt hat. Der eine Radius passte nicht, das hab ich jetzt noch angepasst. Also wenn luxor Boden und Deckel druckt passt das nicht zu dem schon gedruckten Gehäuse, leider. Daher stell ich die STL Datein noch mal neu rein. Hab mal einen Stapel gebaut, bestehend aus DC, Servo und Stepper Brick. Oben der Servo Brick mit einem angepassten Deckel. Die Verbindung hab ich auch mit eingebaut.
-
Stimmt, das ist ein problem. Kannst du vielleicht eine kleine Haltestruktur anbringen, oder vielleicht lässt es sich besser drucken wenn es auf einer der Seiten liegt. Vielleicht sogar auf der Seite mit den großen Aussparunben.